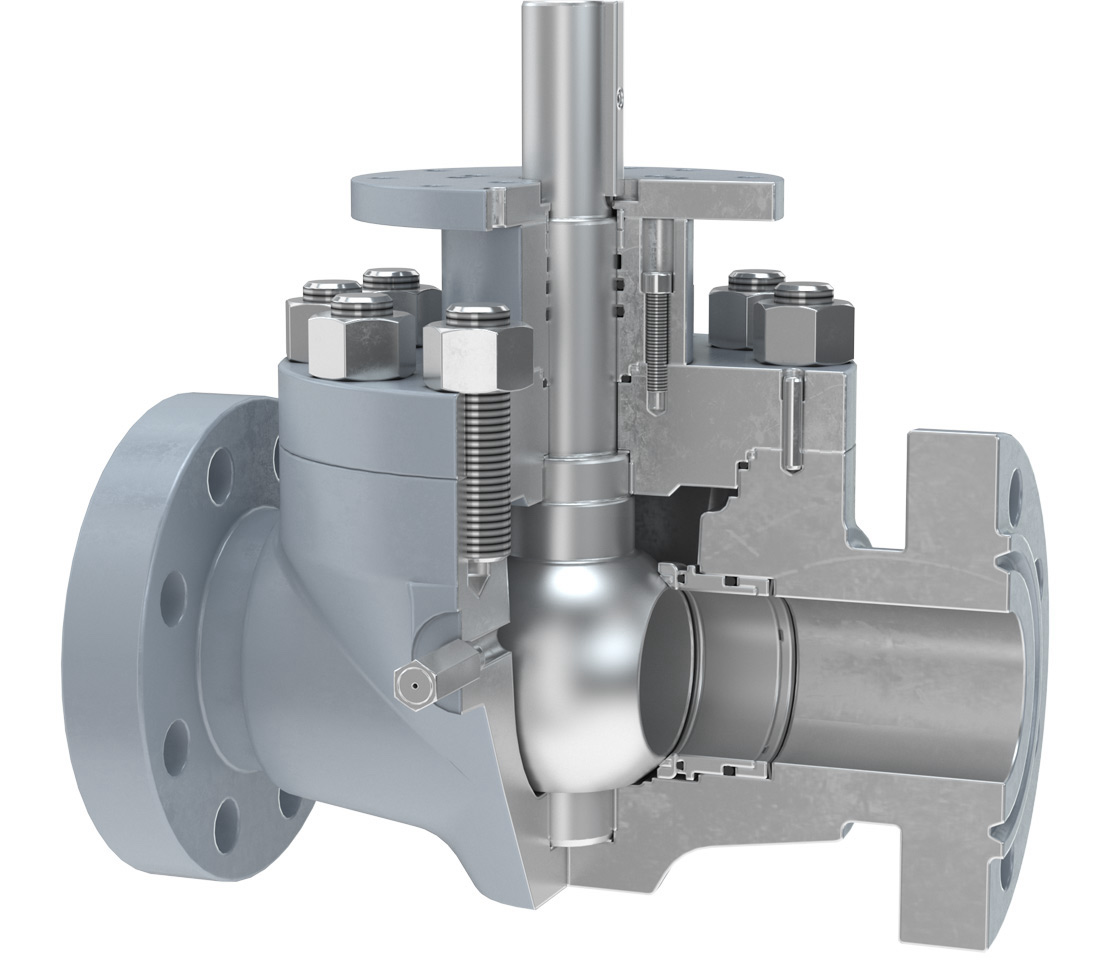
What are the key components of a two way valve –agile ball valve
A two way valve is a fundamental component widely used in various industries, including manufacturing, oil and gas, water treatment, and more. Its primary function is to control the flow of fluids through a pipeline or system.
Understanding the key components of a two way valve is crucial high pressure ball valve for comprehending its operation and maintenance. In this article, we will explore the essential components that make up a two way valve, highlighting their roles and significance in ensuring efficient fluid control.
Body and Bonnet
The body and bonnet serve as the outer shell of a two way valve, providing structural integrity and housing the internal components.
Typically, they are made of durable materials such as cast iron, stainless steel, or bronze, chosen based on the specific application requirements and the fluid being handled.
The body and bonnet are designed to withstand high pressures and temperatures and are often flanged or threaded to facilitate easy installation into a pipeline.
Disc or Plug
The disc or plug is a crucial component responsible for controlling the flow of fluid through the valve. It is located within the valve body and moves in response to the actuator’s commands.
The disc can take various forms, such as a flat plate, spherical shape, or cone, depending on the specific valve design. When the valve is open, the disc allows fluid to flow through the passage, while in the closed position, it seals the passage, preventing any flow.
Seat
The seat is the sealing surface where the disc or plug comes in contact when the valve is in the closed position. It ensures a tight seal, preventing leakage when the valve is closed.
The seat is typically made of a resilient material such as rubber, Teflon, or metal alloys, depending on the nature of the fluid and the operating conditions. The seat design is crucial to achieving proper sealing and minimizing friction during the valve’s operation.
Stem
The stem connects the actuator to the disc or plug and transmits the actuator’s motion to control the valve’s position. It is a long, slender component that extends from the actuator through the bonnet and into the valve body.
The stem must be strong and rigid to withstand the forces exerted during valve operation. It is commonly made of stainless steel or other corrosion-resistant alloys to ensure durability and longevity.
Actuator
The actuator is the component responsible for initiating the movement of the disc or plug. It can be manual, electric, pneumatic, or hydraulic, depending on the application and the level of automation required.
Manual actuators are operated by hand, while automated actuators use various energy sources to control the valve remotely. The actuator provides the necessary force to open or close the valve, allowing for precise control over fluid flow.
Packing and Gland
The packing and gland assembly ensures a tight seal around the stem, preventing fluid leakage along the valve shaft. It consists of packing rings made of materials like graphite or Teflon, which are compressed around the stem by a gland nut or follower.
This arrangement maintains the integrity of the seal while allowing the stem to move smoothly during valve operation. Regular inspection and maintenance of the packing are essential to prevent leaks and ensure efficient valve performance.
In addition to the primary components mentioned above, there are other supporting components that contribute to the overall functionality of a two way valve. These include:
Stem Packing Box:
The stem packing box houses the packing and gland assembly. It provides a protective enclosure for the packing, preventing external contaminants from entering and compromising the seal.
The packing box is typically made of a durable material such as stainless steel or cast iron.
Bolts and Nuts:
Bolts and nuts are used to secure the bonnet to the body, ensuring a tight and leak-free connection. They are often made of high-strength materials to withstand the forces exerted on the valve during operation.
Proper tightening of bolts and nuts is essential to maintain the structural integrity of the valve.
Yoke:
The yoke is a bracket-like component that supports the actuator and connects it to the valve body. It provides stability and ensures proper alignment between the actuator and the stem.
The yoke is typically made of a sturdy material such as cast iron or stainless steel to withstand the forces generated during valve operation.
Stem Nut:
The stem nut is a threaded component that engages with the stem and allows manual operation of the valve. When rotated, the stem nut moves the stem, thereby controlling the position of the disc or plug
It is often provided as a backup option in case of actuator failure or for manual operation during maintenance or emergencies.
Additionally, advancements in valve technology have led to the incorporation of innovative features to enhance the performance and functionality of two way valves. These may include:
Anti-Cavitation Trims:
Cavitation is a phenomenon that occurs when the pressure of a fluid drops below its vapor pressure, resulting in the formation of vapor bubbles that collapse with force, causing damage to the valve components.
Anti-cavitation trims are specially designed components that mitigate the effects of cavitation, prolonging the valve’s lifespan and reducing maintenance requirements.
Positioners:
Positioners are devices that precisely control the valve’s position based on input signals from sensors or controllers. They ensure accurate and responsive valve positioning, enabling precise flow control and optimizing system performance.
Smart Valve Technology:
With the advent of the Internet of Things (IoT), valves can now be equipped with sensors and connectivity features, allowing remote monitoring, control, and data collection.
Smart valve technology enables predictive maintenance, real-time monitoring of valve conditions, and integration with control systems for enhanced automation and efficiency.
Flow Control Mechanisms:
Some advanced two way valves incorporate flow control mechanisms such as throttling devices or flow restrictors to precisely regulate the flow rate and maintain system stability.
These mechanisms can be particularly useful in applications where flow modulation is required.
By keeping up with the latest advancements in two way valve technology, industries can benefit from improved efficiency, reduced downtime, and enhanced system performance.
Conclusion
A two way valve consists of several key components that work together to control fluid flow. Understanding the roles and significance of these components is crucial for proper installation, operation, and maintenance of the valves.
With advancements in technology, additional features and innovations have been incorporated to optimize valve performance and provide greater control and reliability.
By staying informed about these developments, industries can leverage the full potential of two way valves and achieve efficient and sustainable fluid control in their respective applications.