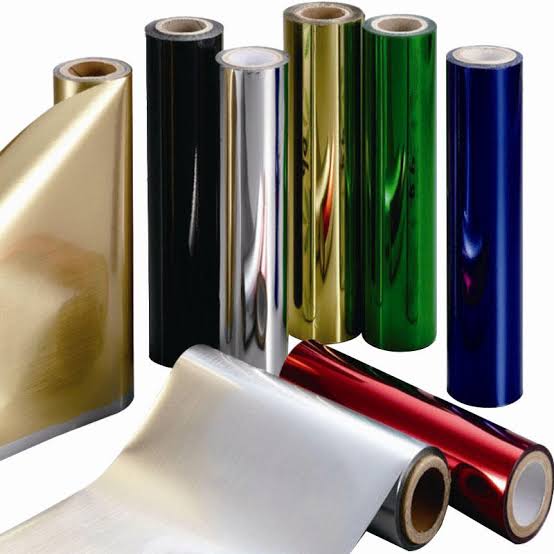
What applications exist for metalized PET film?
Powdered aluminum is an ingredient used in PET met polyester film manufacturing. This component of the film is employed as a component. Polyester film, often referred to as PET film for its acronym in full, differentiates itself rapidly from other films due to its outstanding toughness and surface hardness. This is because polyester has a higher molecular weight than polyethylene, a polyethylene component. This is because the polyester film is made of polyethylene terephthalate and polyester. The reason for this is that polyester film is created out of polyester. However, one of how the beneficial properties may be increased is by increasing aluminum powder, specifically the diffusion density. Who can do this in several ways? One of the valuable characteristics may be boosted by the one described below. This is one way to improve upon the favorable characteristics to a greater degree.
China Metalized Bopet film suppliers that have been metalized using aluminum powder rather than the more typical process of using aluminum foil carry several benefits in addition to a few drawbacks compared to the more common practice of using aluminum foil. This is because metalizing PET film using aluminum powder rather than the more typical aluminum foil approach carries several benefits. The lower costs linked with PET’s production and its better tensile strength are two of the most evident advantages of this material. Another benefit related to this material is its lower coefficient of thermal expansion. The additional flexibility that comes along with using this material is another benefit that comes with using it. When compared to aluminum foil, the processing speed potential of the vaporized aluminum composite material is much higher than that of aluminum foil.
Because of this, PET met, the metalized polyester film, is ideal for uses like:
- Foods that spoil quickly due to exposure to oxygen or moisture need special packaging.
- Insulate a structure using a relative vapor barrier.
- High-temperature and chemical-resistant labels and tapes for use in vehicles and other mobile technologies.
The density of diffusion is high but not absolute
The diffusion, as mentioned earlier, values are obtained when PET met is used as the diffusion medium. These observations are already reasonably close to falling under the measurement limits needed to estimate the absolute diffusion density. This is because these restrictions are necessary to calculate the total diffusion density. Establishing a set of limitations was an essential step in quantitatively analyzing diffusion.
You will need some regular aluminum or any other metal foil to test the diffusion density.
However, you must use regular aluminum or another metal foil to get the maximum feasible diffusion density.
It’s only a hint of metallic silver
Because the layer of aluminum in PET met is so thin, the atomic diameter-derived unit angstrom is sometimes employed in place of the millimeter. (micrometers).
The distance between two places equal to the number of atoms heaped on top of each other is the definition of an angstrom. This distance is measured in angstroms. This is an excellent illustration of the metal base layer’s thickness, although it does not correspond to reality.
Metalized PET film layer thicknesses in absolute terms and comparison
Depending on the overall thickness of the film (which may be anywhere from 30 microns to 500 microns), the aluminum layer in a metalized PET film may generally vary from 3 to 50 nanometers. The overall film thickness may range from 30 to 500 microns, explaining the size range. One ounce of pure gold may be processed into two-thousandths of an inch of thin gold leaf as a comparison. You can see how delicate gold leaf can be. This is only one illustration among countless more. When held up to the light, gold of this thickness appears green and gives the impression of being slightly translucent.
There is usually some opacity to PET met foil
Even by using metalized PET film, it is not possible to conceal anything entirely. When the light that lights it is reflected off of the item’s surface, which is silvery, this effect is altogether nullified. Brushing, embossing, printing, dying, and varnishing are just a few of the many processes that may use to change the texture of the surface of a PET film. Other methods include brushing, die-cutting, and printing.
Sun and heat rays are effectively blocked
A metalized PET film’s highly reflective surface may be utilized to provide an appealing visual appearance in packaging and to function as a shield against electromagnetic radiation.
PET foil with an aluminum vapor coating effectively reflects all light wavelengths, including ultraviolet rays. When compared to silver or gold, aluminum coatings serve a different function. Aluminum’s reflectance is far less wavelength dependant than that of the other metals. The near-infrared minimum is slightly over 800 nm, which is still around 85%.
The thickness of the layer has an impact on the PET material’s reflectivity
The optical density and the reflection factor are positively impacted by an increase in the thickness of the aluminum coating applied to the metalized PET film. This coating is responsible for the metallic appearance of the film. Aluminum has a high refractive index, which is why this is the case. The optical density (OD) of PET material will typically fall between 0.25 to 3.5 most of the time. What may do quantifying optical density in a few different ways. One method involves taking the logarithm of the ratio between the amount of radiation energy that is transmitted and the quantity of incoming radiation.
Thicker aluminum layers increase optical density and decrease transparency
Because the logarithmic scale is used, an optical density of 0.3 is equivalent to half of the intensity of the transmitted light; hence, the degree of reflection is between 66% and 99%. Because the logarithmic scale is used, the optical density of 0.3 is equivalent to half of the intensity of the transmitted light.
Effects of Aging on Attributes
The aluminum-coated PET film undergoes surface oxidation, much like pure solid aluminum. The side facing the air and the substrate side is shielded from additional chemical change.
The optical density and electrical conductivity of metalized PET films degrade rapidly during the first 24 hours of manufacturing due to self-passivation caused by the creation of transparent aluminum oxide. Who must consider this factor throughout manufacturing to ensure that the values specified by the client are met?
Transparency in PET-met films improves with time
Because the oxide layer only increases to a maximum of 3 to 4 nm in thickness regardless of the thickness of the China Aluminum Foil manufacturers coating, the impact is especially apparent with thin coatings. Within twenty-four hours, the optical density may decline from 0.2 to 0.28 when an aluminum coating of around 10 nm thick is applied, and over time, it can drop to nearly half of the value it was initially.
Common uses of metal-coated PET film
Metalized PET film may be used in the packaging industry as an alternative to aluminum foil. PET met has more tensile strength and flexural stiffness than aluminum foil of the same film thickness, making the composite material created by the vaporization of the metal less prone to wrinkles.
Alternatives to Alu and the Benefits and Drawbacks of Using PETmet
This may help the package seem more professional. Despite this, metalized PET film may also be used to create individual candy packets with a closure that relies on twisting the film ends together (twist closure).
However, unlike PET met film, aluminum foil provides an absolute diffusion density and is opaque, giving it an advantage in particular containers. This means PET-assembled film is less long-lasting than aluminum foil when preserving food. Therefore, PET met film is more suited for perishable commodities that spend less time in the shop before being purchased.
Because the skinny metal coating modifies the film’s surface electrical conductivity, metalized PET film opens up new options for use in food packaging. This makes microwaveable foods with low water content more detectable by metal detectors and allows the food to absorb more microwave energy and heat up faster in the package.
The favorable effect of aluminum vaporization on diffusion resistance and thermal radiation reflection is significant in the context of building insulation. While PET met lacks the ultimate vapor barrier of aluminum foil, it outperforms metal in mechanical resistance and reflectivity.