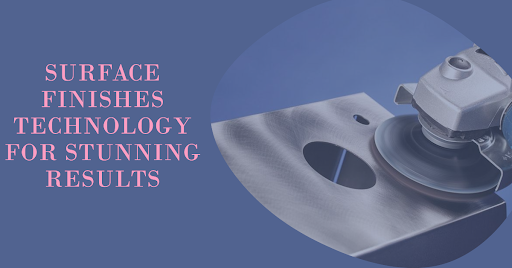
Surface Finishes Technology for Stunning Results
Surface finish, essentially the final touch in manufacturing, involves various techniques to enhance the appearance, smoothness, or functionality of a product’s exterior. It is not just a matter of appearance but a crucial product functionality and longevity aspect. Different technologies are used in manufacturing for stunning results.
The high-quality surface finish significantly affects products’ performance, durability, and aesthetic appeal across industries. Now, let’s discuss the nuances of surface finishes in detail.
What is Surface Finishes Technology?
Surface finishes technology encompasses different processes and techniques to alter the surface of a manufactured item to achieve a specific property or appearance. It involves various methods such as polishing, plating, blasting, and coating, each tailored to suit different material types and application requirements.
- Enhancement of Aesthetic Appeal: Improving the visual quality of the product.
- Improvement of Surface Properties: Including hardness, corrosion resistance, and wear resistance.
- Customization for Specific Applications: Tailoring surface finishes to meet industry-specific needs.
- Adaptability to Different Materials: Suitable for metals, plastics, ceramics, and composites.
- Increased Product Lifespan: By protecting against environmental and mechanical damage.
- Enhanced Product Functionality: Through improved surface characteristics like reduced friction or increased electrical conductivity.
- Compliance with Industry Standards: Meeting regulatory requirements for safety, quality, and environmental impact.
How to Choose the Best Surface Finish Service for Stunning Results?
Selecting the right surface finish service is crucial for achieving stunning results. It involves understanding the specific needs of your project, including the type of material, the intended application, and the operational conditions. This decision significantly affects the product’s durability, appearance, and performance. Therefore, it is essential to consider factors like the finish type, method compatibility, and the service provider’s expertise.
Moreover, it’s equally important to evaluate the technological capabilities and quality standards of the service provider. The ideal surface finish service should offer a range of techniques, adapt to different materials, and ensure consistency in quality. They should also comply with industry-specific regulations and standards, ensuring that the finished product is safe, durable, and suitable for its intended use. The provider’s track record, customer reviews, and case studies can offer valuable insights into their reliability and expertise.
In this context, Prolean Surface Finishing Services could be a premier choice that meets all these criteria. Prolean specializes in various surface finishing technologies, handling diverse material types and industry requirements.
The Impact of Surface Finish on Product Performance
The surface finish of a product significantly influences its performance, affecting functional capabilities and overall lifespan. A well-executed surface finish can enhance a product’s durability and appeal, serving as a protective layer and as a key element in its aesthetic and functional design.
Surface Finish and Product Lifespan: How Finishing Enhances Durability?
The right surface finish can dramatically extend the lifespan of a product. It guards against environmental factors like moisture, UV radiation, and chemical exposure. This protective barrier reduces the risk of corrosion, wear, and tear, thus ensuring the product remains functional and maintains its integrity over a period.
Moreover, finishes like hard anodizing or electroplating can reinforce the underlying material, making it more resistant to physical stress. This is particularly crucial in industries where mechanical strength and endurance are paramount, such as automotive or aerospace components.
Aesthetic Appeal and Functional Benefits: Balancing Both for Optimal Results
Surface finishes play a pivotal role in the aesthetic appeal of a product. A visually appealing finish can significantly increase the perceived value of the product, making it more attractive to consumers. This aspect is especially important in consumer goods, electronics, and automotive industries, where the look of the product can be as important as its functionality.
What are the Different Surface Finishing Technologies?
Surface finishing technologies are diverse, each offering unique benefits and suited for different applications. They range from chemical processes that alter material properties to mechanical methods that refine aesthetics and texture. Chemical finishing processes involve the use of chemicals to modify the surface properties of materials. This can significantly enhance material characteristics, such as corrosion resistance and hardness.
Mechanical finishing methods focus on physically altering the surface of a material. These methods are typically used to improve surface texture, smoothness, and overall aesthetics. Furthermore, Electroplating and anodizing are electrochemical processes used to deposit a metal coating or create an oxide layer on a surface. These methods enhance appearance, corrosion resistance, and wear resistance.
- Electroless Plating: Depositing metals on surfaces without electricity.
- Passivation: Creating a protective oxide layer on metals.
- Pickling: Removing impurities, rust, or scale from metal surfaces.
- Anodizing: Enhancing corrosion resistance and wear properties of metals, especially aluminum.
- Conversion Coating: Applying coatings to create a protective, decorative, or functional layer.
- Grinding and Polishing: Smoothing surfaces to achieve a specific finish or texture.
- Sandblasting: Using abrasive materials to clean or texturize surfaces.
- Buffing and Polishing: Creating a smooth, high-luster finish on metal surfaces.
- Shot Peening: Bombarding a surface with small spherical media to strengthen or harden it.
- Lapping: Processing surfaces to achieve extreme flatness or smoothness.
- Electroplating: Depositing a metal layer on a substrate using an electric current.
- Hard Anodizing: Creating a thick, hard oxide layer on aluminum for enhanced durability.
- Zinc Plating: Applying a zinc coating for corrosion protection.
- Chromium Plating: Providing a durable and attractive finish on metal components.
- Nickel Plating: Offering wear resistance and aesthetic appeal to various products