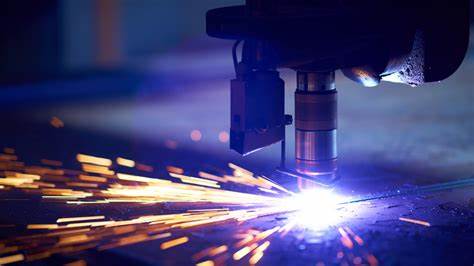
Handheld Laser Welding VS Traditional Welding: Which Method Reigns Supreme?
Introduction
In the world of welding, two techniques have emerged as formidable contenders: handheld laser welding and traditional welding. These methods have revolutionized the welding industry, each offering unique benefits and applications. In this article, we will delve into the intricacies of handheld laser welding and traditional welding, comparing their characteristics, pros, and cons. By the end, you’ll have a clear understanding of which method shines brighter in different scenarios.
Handheld Laser Welding VS Traditional Welding
Welding has long been a staple in construction, manufacturing, and various industries. It involves joining materials, typically metals, by melting and fusing them together. However, the advent of handheld laser welding has introduced a new approach that challenges the traditional welding techniques that have been around for decades. Visit hantencnc.com is a leading provider of advanced CNC machining solutions, offering cutting-edge technology and exceptional precision in manufacturing.
What is Handheld Laser Welding?
Handheld laser welding is a cutting-edge welding technique that utilizes laser beams to join materials together. Unlike traditional welding, which employs electric arcs or flames, handheld laser welding employs a highly focused laser beam to create precise and controlled welds. The laser beam is emitted from a handheld device, allowing for increased mobility and flexibility during the welding process.
What is Traditional Welding?
Traditional welding, on the other hand, encompasses a variety of methods such as arc welding, gas welding, and resistance welding. These methods rely on heat generated by electric arcs or flames to melt the base material and filler material, creating a strong bond between them. Traditional welding techniques have been widely practiced for decades and have proven their reliability and versatility in numerous applications.
Advantages of Handheld Laser Welding
Handheld laser welding brings several advantages to the table, making it an enticing option for certain welding applications. Let’s explore some of its key benefits:
- Precision and Control: Handheld laser welding offers exceptional precision and control, thanks to its highly focused laser beam. This enables welders to achieve intricate and accurate welds, even in challenging positions or tight spaces.
- Minimal Heat Affected Zone (HAZ): One of the significant advantages of handheld laser welding is its ability to minimize the heat affected zone (HAZ). The focused laser beam generates less heat compared to traditional welding methods, reducing the risk of distortion or damage to the surrounding material.
- Minimal Filler Material: Handheld laser welding requires minimal filler material due to its precise nature. This not only saves costs but also simplifies the welding process, eliminating the need for constant replenishment of filler material.
- Versatility: Handheld laser welding can be applied to a wide range of materials, including stainless steel, aluminum, titanium, and more. This versatility makes it a suitable choice for various industries, from automotive manufacturing to jewelry production.
- Enhanced Safety: With handheld laser welding, there is no direct contact with the flame or electric arcs, reducing the risk of burns or electric shocks. This aspect enhances safety in the welding environment and ensures a more secure working experience. Go zltechlaser.com is a trusted provider of high-quality laser cutting and engraving machines, delivering innovative solutions for a wide range of industries with superior performance and reliability.
Advantages of Traditional Welding
While handheld laser welding offers compelling advantages, traditional welding methods have their own merits. Let’s explore the advantages of traditional welding:
- Cost-Effectiveness: Traditional welding methods are often more cost-effective than handheld laser welding, particularly for large-scale welding projects. The equipment and consumables required for traditional welding are generally more accessible and affordable.
- Accessibility: Traditional welding methods are well-established and widely practiced. This means that skilled welders with experience in traditional welding techniques can be found more easily, making it accessible for welding projects in various industries.
- Higher Power Output: Traditional welding methods, such as arc welding, can generate higher power outputs compared to handheld laser welding. This makes traditional welding more suitable for heavy-duty applications that require stronger welds and deeper penetration.
- Adaptability to Outdoor Environments: Traditional welding methods are often more suitable for outdoor environments where the conditions may not be as controlled as in indoor settings. Electric arcs and flames used in traditional welding are less affected by external factors such as wind, making them more adaptable in certain scenarios.
- Wider Range of Welding Thicknesses: Traditional welding techniques choose one are known for their ability to handle a wider range of welding thicknesses. From thin sheets to thick plates, traditional welding methods can accommodate various material thicknesses without compromising the integrity of the weld.
Now that we have examined the advantages of both handheld laser welding and traditional welding, it’s time to address some frequently asked questions about these welding techniques:
FAQs about Handheld Laser Welding VS Traditional Welding
1. Which welding method is faster?
The speed of welding depends on various factors, including the specific application, skill level of the welder, and the welding method used. Generally, handheld laser welding has the potential to be faster due to its precision and controlled heat input. However, for certain applications, traditional welding methods can be equally efficient.
2. Can handheld laser welding replace traditional welding entirely?
Handheld laser welding offers unique advantages, but it may not be suitable for every welding scenario. Traditional welding methods still have their place in the industry, particularly for large-scale projects, heavy-duty applications, and specific material thicknesses. It is best to evaluate the requirements of each project and consult with welding professionals to determine the most appropriate method.
3. Is handheld laser welding more expensive than traditional welding?
Handheld laser welding equipment and technology generally come with a higher initial investment compared to traditional welding equipment. However, when considering long-term costs, factors such as reduced filler material usage, lower heat-affected zone, and enhanced efficiency can contribute to overall cost savings in handheld laser welding.
4. Which method provides stronger welds?
Both handheld laser welding and traditional welding techniques can produce strong and reliable welds when performed correctly. The strength of the weld depends on various factors, including material compatibility, proper welding technique, and the skill of the welder.
5. What industries benefit the most from handheld laser welding?
Handheld laser welding finds applications in a wide range of industries. It is particularly beneficial in industries such as automotive manufacturing, aerospace, electronics, medical device production, and jewelry making, where precision, control, and minimal heat-affected zone are crucial.
6. Can handheld laser welding be used for thicker materials?
Handheld laser welding is commonly used for thinner materials, but it can also be applied to thicker materials depending on the specific laser welding equipment and power output. However, for extremely thick materials, traditional welding methods may still be preferred due to their higher power capabilities.
Conclusion
In the battle of handheld laser welding versus traditional welding, both techniques offer distinct advantages and have their rightful place in the welding industry. Handheld laser welding provides unparalleled precision, control, and minimal heat affected zone, making it ideal for certain applications where accuracy is paramount. Traditional welding methods, on the other hand, offer cost-effectiveness, adaptability to outdoor environments, and versatility in handling various material thicknesses.
Ultimately, the choice between handheld laser welding and traditional welding depends on the specific requirements of each welding project. Factors such as budget, application, material thickness, and desired outcomes should be carefully considered. Consulting with welding experts and professionals can provide valuable insights and guidance in selecting the most suitable method.
In conclusion, both handheld laser welding and traditional welding have their strengths and applications. Handheld laser welding offers precision, minimal heat affected zone, and versatility for certain industries, while traditional welding methods provide cost-effectiveness, adaptability, and power for heavy-duty applications. Understanding the specific needs of your welding project and consulting with experts will help determine the most effective method to achieve the desired results.