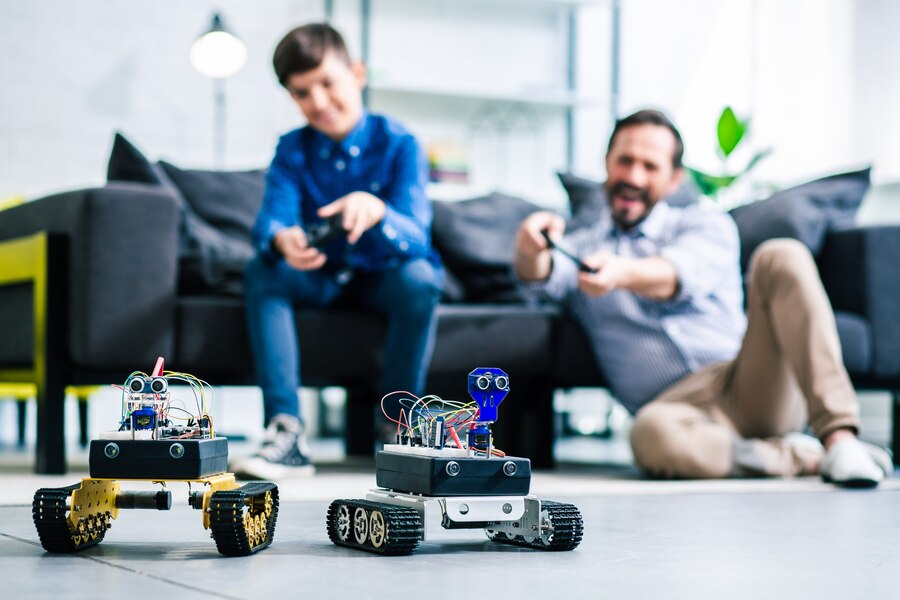
A Comprehensive Guide On AMR (Autonomous Mobile Robot)
Today, most businesses are moving towards automation. Increasing production rates and productivity, optimizing resource utilization, enhancing product quality, and cutting manufacturing lead times are typical objectives across most sectors.
People have multiple options for robotics, including an AMR (autonomous mobile robot).
Autonomous mobile robots are revolutionizing the field of automation. These robots swiftly navigate through large warehouses, transporting newly purchased items for delivery worldwide. They are taking over the role of forklifts, effortlessly moving payloads weighing up to thousands of kilograms around factory floors.
Autonomous Mobile Robot Architecture
Autonomous mobile robots are sophisticated products that integrate hardware, software, and specialized components. These devices are typically classified based on their navigation capabilities, including localization, navigation, and motion planning, which determine their level of autonomy. However, there is a more profound complexity to AMR beyond just their navigation capabilities; navigation is just one aspect of their functionality.
- Hardware: Wheels, brakes, motors, encoders, batteries, and sensors are the main physical elements in AMRs. Other crucial hardware elements may include chassis, actuators, control units, communication modules, cameras, and manipulators. These components work in tandem to enable AMRs to navigate, perceive their environment, and execute tasks autonomously.
- Software: The software functionality of Autonomous Mobile Robots encompasses various aspects such as scanning, visual processing, and recognizing designated areas and endpoints on conveyors. It also includes managing material reception and delivery and providing control and device management capabilities.
Localization, navigation, and motion planning are central to the software and are essential for AMR’s operations. This core functionality lets the robot determine its position and move safely along predefined paths. Depending on the requirements, the AMR software may employ different navigation strategies, ranging from simple line following to complex environment mapping and obstacle avoidance. Additionally, software design involves creating interfaces for human interaction.
To execute these functions effectively, AMRs rely on diverse sensors, including lidar, infrared sensors, cameras, accelerometers, lasers, and ultrasound sensors. The choice of sensors influences both the navigation capabilities and the overall cost of the robot.
Navigation capabilities are a significant factor distinguishing AMRs, impacting functionality and cost. The AMR manufacturer may develop these functionalities in-house or outsource them to third-party developers.
Keys To The Success Of AMR (Autonomous Mobile Robot)
Successful use of AMR depends on some key factors:
- Robot operating system (ROS)
According to data, 55% of all robot sales in 2024 are projected to use ROS. ROS is a comprehensive set of tools and frameworks for developing robotic applications. Despite its name, ROS is not a robot or an operating system per se; instead, it is a crucial component in AMR projects.
Open Robotics’ ROS comprises tools, libraries, and conventions that facilitate rapid development by allowing developers to leverage existing work. While ROS 1 initially lacked certain features essential for industrial robot projects—such as mission-critical security, integration with other robots and operational technology, and scalability—the demand for these capabilities led to the development of ROS 2, the preferred choice for industrial AMR projects.
- Open source technologies
Proprietary technologies can hinder the realization of full AMR functionality and interoperability with other systems. In contrast, open-source technology fosters a connected ecosystem where data flows freely between robots, industrial equipment, systems, the cloud, applications, and people.
- Edge computing
AMR requires rapid processing of large volumes of data from various sources to operate accurately and reliably. These inputs encompass AI vision, LiDAR and sensors, and communication with other robots and industrial systems.
To make split-second decisions and ensure safe human interaction, AMRs must compute continuously in real-time. While cloud computing facilitates data management and training, edge computing enables robots to operate autonomously with minimal latency.
Companies are already leveraging AMR (autonomous mobile robots). Keeping up with the latest developments in hardware and software is crucial for organizations hoping to utilize these revolutionary technologies fully in their operations.
Prime Robotics – The Best In Robotics
Are you looking for the best AMR (autonomous mobile robot) for your warehouses? Prime
Robotics is the ultimate place for your warehouse automation needs.
Boost your warehouse productivity further with Prime Robotics’ Dynamic Pick and Palletizing Arm. This versatile, high-speed solution seamlessly integrates with the AMR solutions and software, enabling multi-box picking, moving payloads of up to 290 pounds, and picking cases at a rate of up to 900 per hour.
Visit the website and find other AMR solutions that meet your needs and requirements. In addition to AMR, you can find a range of different robots, and tools.