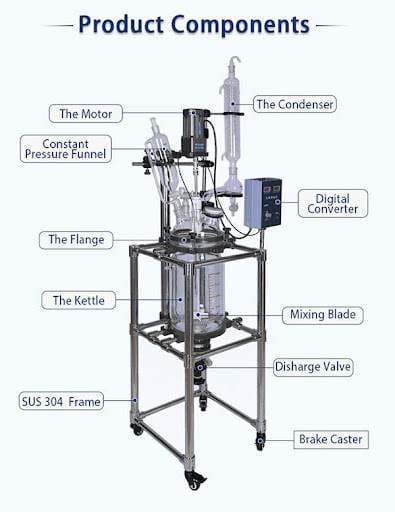
What Is A Pilot Plant Glass Reactor
A pilot plant glass reactor is a type of glass reactor that is designed for use in pilot-scale chemical production. It is a larger version of a laboratory glass reactor and is typically used for testing new processes or scaling up processes from the laboratory to the pilot plant level.
Pilot plant glass reactors are commonly used in the chemical, pharmaceutical, and biotechnology industries, among others. They typically have a capacity of several liters to tens of liters and are designed to withstand higher pressures and temperatures than laboratory glass reactors. They are also equipped with additional features, such as multiple ports for sampling and feeding, and advanced control systems for monitoring and controlling the reaction parameters.
Features of pilot glass reactor
The design and construction of pilot plant glass reactors are important factors in ensuring their safety and reliability. They are typically made of borosilicate glass or other materials that are resistant to corrosion and thermal shock. They may also be equipped with safety features, such as pressure relief valves and temperature sensors, to prevent accidents and ensure safe operation.
Pilot plant 5l glass reactor is an important tool for process development and optimization in the chemical industry, allowing for the testing and scaling up of new processes before full-scale production.
Pilot plant glass reactors are also used to study the effects of different reaction conditions, such as temperature, pressure, and mixing speed, on the product yield and quality. This information can then be used to optimize the process parameters for full-scale production.
In addition to their use in process development and optimization, pilot plant glass reactors are also used for producing small quantities of specialty chemicals, such as pharmaceutical intermediates, that may not be economical to produce on a large scale.
Pilot plant glass reactors can be operated in a variety of modes, including batch, semi-batch, and continuous modes. In batch mode, the reactants are added to the reactor vessel all at once, and the reaction proceeds until completion. In semi-batch mode, one or more of the reactants are added incrementally during the reaction. In continuous mode, the reactants are continuously fed into the reactor vessel, and the products are continuously withdrawn, allowing for continuous production.
Application of pilot glass reactor
Pilot plant 5l glass reactor is often customized to meet the specific needs of different industries and applications. For example, in the pharmaceutical industry, pilot plant glass reactors may be used for developing new drug formulations, optimizing process parameters for drug synthesis, and producing small quantities of drug substances for clinical trials.
In the chemical industry, pilot plant glass reactors are used for developing new chemical processes, optimizing process parameters, and producing small quantities of specialty chemicals for niche markets. They can also be used for testing the feasibility of new chemical processes, including those that involve hazardous materials.
Some pilot plant glass reactors are also equipped with advanced control systems that allow for precise control of reaction conditions. For example, temperature, pressure, and mixing speed can be controlled and monitored using sophisticated control algorithms, allowing for greater process control and reproducibility.
Overall, pilot plant glass reactors are an essential tool for process development and optimization in the chemical industry. They allow for the testing and scaling up of new processes before full-scale production, and can also be used for producing small quantities of specialty chemicals. Their use helps to reduce the time and cost of process development, and ensures safe and reliable operation of chemical processes.