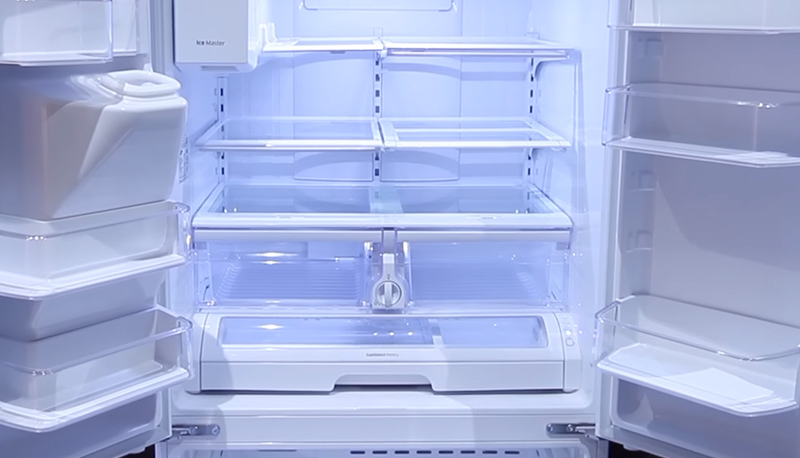
High Gloss Injection Molding: Enhancing Aesthetics and Performance
In today’s competitive market, manufacturers strive to create visually appealing products that stand out from the crowd. One method that has gained significant popularity is high gloss injection molding. This technique allows for the production of plastic parts with a smooth and reflective surface finish, adding a touch of elegance to a wide range of applications. In this article, we will explore the process of high gloss injection molding, its benefits, applications, challenges, and tips for achieving outstanding results.
Introduction
Definition of High Gloss Injection Molding
High gloss injection molding refers to the process of manufacturing plastic components with a glossy, mirror-like surface finish using injection molding techniques. This method involves injecting molten plastic into a precisely designed mold cavity and then rapidly cooling it to solidify the material. The result is a product with a highly polished surface that reflects light and exudes a premium appearance.
Importance of High Gloss Finishes in Plastic Products
The visual appeal of a product plays a crucial role in attracting consumers and influencing their purchase decisions. High gloss finishes add a touch of sophistication and luxury to plastic parts, making them more desirable to customers. Whether it’s the sleek dashboard of a car, the polished casing of a smartphone, or the glossy finish of a kitchen appliance, high gloss injection molding helps elevate the overall aesthetics and perceived value of these products.
The Process of High Gloss Injection Molding
Injection molding is a versatile manufacturing process widely used for producing plastic parts. When it comes to achieving high gloss finishes, several additional considerations come into play.
Explanation of the Injection Molding Process
The injection molding process begins with the preparation of the mold, which consists of two halves: the cavity and the core. High-pressure injection of molten plastic material occurs within the mold. After the material cools and becomes solid, the mold opens, allowing the ejection of the final part. The precision and control offered by injection molding make it an ideal choice for producing parts with high gloss finishes.
Specific Techniques Used for Achieving High Gloss Finishes
To achieve exceptional gloss levels, manufacturers employ various techniques during the injection molding process. One common approach is the use of highly polished molds, which minimize surface imperfections and enhance light reflection. Additionally, mold temperature control, precise material selection, and optimization of processing parameters all contribute to the final gloss quality.
Role of Mold Design and Polishing
Mold design plays a critical role in the attainment of high gloss finishes. Properly designed molds ensure uniform material flow, minimize the occurrence of defects, and facilitate easy ejection of the finished part. Polishing the mold surfaces to a mirror-like finish is another essential step that enhances gloss levels and reduces the likelihood of blemishes.
Benefits of High Gloss Finishes
Enhanced Aesthetic Appeal
One of the primary advantages of high gloss finishes is the visual appeal they bring to products. Glossy surfaces create a sense of luxury and sophistication, making products stand out on store shelves or in promotional materials. Whether it’s a high-end automotive interior or a sleek electronic device, the reflective properties of high gloss finishes evoke a sense of quality and craftsmanship.
Increased Product Value and Marketability
High gloss finishes have the potential to elevate the perceived value of products. Consumers often associate glossiness with premium quality, and as a result, products with glossy surfaces tend to command higher prices in the market. Additionally, a visually striking appearance can attract more attention and generate greater interest among potential buyers, leading to increased sales and market share.
Improved Scratch and Chemical Resistance
Aside from their aesthetic benefits, high gloss finishes also offer practical advantages. The smooth surface of glossy parts tends to be more resistant to scratches, making them suitable for applications where durability is essential. Furthermore, certain resins and coatings used in high gloss injection molding can provide enhanced resistance to chemicals, ensuring the longevity of the finished product.
Applications of High Gloss Injection Molding
The versatility of high gloss injection molding makes it applicable to a wide range of industries and products. Some notable examples include:
Automotive Industry
In the automotive sector, high gloss finishes are extensively utilized for interior components such as dashboards, center consoles, and door panels. The glossy surfaces impart a sense of luxury and refinement to the vehicle’s interior, enhancing the overall driving experience.
Consumer Electronics
From smartphones and laptops to audio equipment and home appliances, high gloss finishes are commonly found in the consumer electronics industry. Glossy casings and touch surfaces not only enhance the aesthetic appeal but also provide a smooth, fingerprint-resistant experience for users.
Household Appliances
Kitchen appliances, home entertainment systems, and various household gadgets often feature high gloss finishes. These glossy surfaces are not only visually appealing but also easy to clean and maintain, making them a preferred choice for busy households.
Medical Devices
In the medical field, high gloss injection molding is used to create parts for devices like diagnostic equipment, surgical instruments, and prosthetics. The reflective surfaces of these components aid in maintaining cleanliness, while the sleek appearance helps create a positive impression on patients and healthcare professionals.
Challenges and Considerations
While high gloss injection molding offers numerous benefits, there are challenges and considerations that manufacturers need to address.
Surface Defects and Imperfections
Attaining a flawless high gloss finish can be challenging due to the potential for surface defects. Factors such as air traps, flow marks, and parting lines can mar the glossy appearance. Manufacturers employ careful mold design, precise processing parameters, and thorough quality control to minimize such defects.
Material Selection for High Gloss Finishes
Not all plastic materials are suitable for high gloss injection molding. Manufacturers must consider factors like resin transparency, flow characteristics, and heat resistance. Common materials used for high gloss finishes include ABS, PC/ABS blends, and acrylics.
Post-processing and Quality Control
After the injection molding process, additional steps may be necessary to further enhance the glossiness of the parts. These steps may include secondary polishing, buffing, or applying protective coatings. Strict quality control measures are also crucial to ensure consistency in gloss levels across the produced parts.
Tips for Achieving High Gloss Finishes
Manufacturers can employ several techniques to optimize their high gloss injection molding process and achieve outstanding results.
Proper Mold Surface Preparation
Thorough mold surface preparation, including polishing and appropriate surface treatments, is essential to achieve high gloss finishes. This step helps eliminate imperfections, enhance surface smoothness, and promote better light reflection.
Optimization of Injection Molding Parameter
Precise control of injection molding parameters such as temperature, pressure, and cooling time is crucial for obtaining consistent high gloss finishes. Fine-tuning these parameters can minimize defects and optimize the flow of molten plastic, resulting in superior gloss quality.
Use of High-Quality Resins and Additives
Selecting high-quality resins with excellent optical properties and adding appropriate additives can significantly impact the final gloss performance. Manufacturers should consider using resins specifically formulated for high gloss applications and incorporating additives that improve flow, reduce surface tension, or enhance scratch resistance.
Advancements in Surface Treatment Technologies
New surface treatment technologies, such as plasma coating and vapor deposition, are emerging to enhance the gloss and scratch resistance of high gloss finishes. These innovative techniques provide additional options for manufacturers to achieve superior results.
Integration of Smart Functionalities with High Gloss Finishes
The integration of smart functionalities, such as touch-sensitive surfaces and embedded sensors, with high gloss finishes is an exciting area of development. This combination allows for the creation of sleek and interactive products that blend technology with aesthetics.
Conclusion
High gloss injection molding offers manufacturers a powerful tool to elevate the visual appeal and perceived value of their products. The glossy surfaces impart sophistication and elegance, making them highly desirable in various industries such as automotive, consumer electronics, household appliances, and medical devices. By understanding the process, benefits, challenges, and best practices associated with high gloss finishes, manufacturers can unlock new opportunities for innovation and market differentiation.
Frequently Asked Questions (FAQs)
Q: How durable are high gloss finishes?
A: High gloss finishes can be highly durable, especially when using scratch-resistant coatings or selecting materials with excellent mechanical properties. However, proper care and maintenance are still necessary to preserve the glossy appearance over time.
Q: Can any plastic material be used for high gloss injection molding?
A: Not all plastic materials are suitable for achieving high gloss finishes. Transparent and amorphous resins like ABS, PC/ABS blends, and acrylics are commonly used due to their optical properties and ability to achieve glossy surfaces.
Q: Is high gloss injection molding cost-effective?
A: The cost-effectiveness of high gloss injection molding depends on various factors such as part complexity, material selection, and finishing requirements. While the process may have higher upfront costs compared to standard injection molding, the added value and marketability of glossy parts can often justify the investment.
Q: Can high gloss finishes be applied to large parts?
A: Yes, high gloss finishes can be applied to both small and large plastic parts. However, larger parts may present additional challenges due to the potential for uneven cooling and increased difficulty in achieving consistent gloss levels across the entire surface.
Q: What are the limitations of high gloss injection molding?
A: High gloss injection molding has some limitations, including the potential for surface defects, the need for precise process control, and the requirement for specific material properties. Additionally, glossy surfaces may be more prone to showing fingerprints and scratches, requiring careful handling and maintenance.