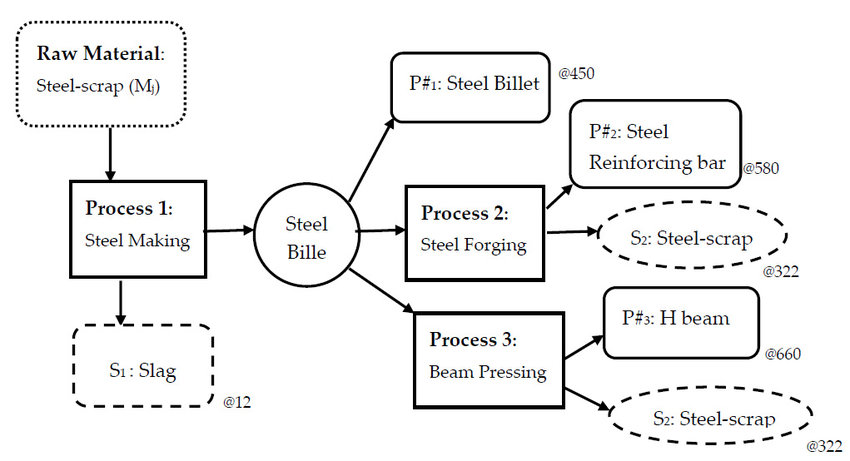
From raw material to construction: An in-depth look at the steel manufacturing process
Steel is an integral part of the modern-day infrastructure, from buildings to bridges and everything in between. It is one of the most widely used materials in construction, manufacturing, and other industries. It is an alloy made primarily of iron and carbon, adding small amounts of other elements added to achieve specific properties. The manufacturing process of steel is a fascinating and complex journey that starts with raw materials and results in finished products used in construction projects worldwide. In this blog post, we’ll take a deep dive into the steel manufacturing process, exploring the various stages involved, from the sourcing of raw materials to the construction of the final product.
Steps involved in the steel manufacturing process
The steps involved in the steel manufacturing process are as follows-
Sourcing raw materials
The first step in the steel manufacturing process is obtaining the raw materials. The primary raw material used in steel production is iron ore. Other materials include limestone, coal, and recycled steel scrap. These materials are transported to the steel plant and stored in designated areas.
Ironmaking
The next step in the steel manufacturing process is ironmaking. This involves the conversion of iron ore into iron. The most common method for ironmaking is the blast furnace process. In this process, iron ore, coke (a form of coal), and limestone are added to the furnace. The coke burns to produce carbon monoxide, which reduces the iron ore to iron. Finally, the limestone reacts with impurities in the iron ore to form slag, which is removed from the furnace.
Steelmaking
After ironmaking, the next step is steelmaking. This involves converting the iron into steel by adding small amounts of carbon and other elements. There are two primary methods for steelmaking: the basic oxygen furnace (BOF) and the electric arc furnace (EAF).
In the BOF process, molten iron from the blast furnace is transferred to a vessel where oxygen is blown into the molten iron to remove impurities. This process results in the production of steel.
- In the EAF process, recycled steel scrap is melted in an electric arc furnace. The scrap is heated to high temperatures using an electric arc, and other materials such as limestone and alloys are added to achieve the desired properties. This process is more environmentally friendly than the BOF process since it uses recycled steel scrap.
Casting
Once the steel has been produced, it is cast into various shapes and sizes. The most common method for casting steel is the continuous casting process. In this process, the steel is poured into a water-cooled mould and cooled until it solidifies. And finally, the solidified steel is then cut into various lengths and sizes.
Finishing
After casting, the steel is sent to the finishing process, where it is cleaned and prepared for use. The finishing process involves various steps, including hot rolling, cold rolling, annealing, and pickling.
Hot rolling involves passing the steel through a series of rollers at high temperatures. This process shapes the steel into various forms, including sheets, bars, and plates.
Cold rolling involves passing the steel through a series of rollers at lower temperatures. This process results in a smoother surface and tighter tolerances.
Annealing involves heating the steel to high temperatures and then slowly cooling it. This process improves the steel’s ductility and toughness.
- Pickling involves removing any remaining impurities or scale from the surface of the steel.
Final product
Once the finishing process is complete, the steel is ready to be used for various applications. Steel is used in many industries, including construction, automotive, and manufacturing. It can be formed into various shapes and sizes to meet specific needs.
- In construction, steel is used for structural applications such as beams, columns, and trusses. It is also used for reinforcing concrete and for roofing and siding.
- In the automotive industry, steel is used for car bodies, frames, and components.
- In manufacturing, steel is used for machinery, tools, and equipment.
Conclusion
The steel manufacturing process is a complex and multi-step process that involves a range of different techniques and technologies. From mining and refining the raw materials to forming and finishing the final product, every step is essential to producing high-quality steel for use in construction and manufacturing.
It is one of the most important materials in modern society, and its versatility and strength make it ideal for a wide range of applications. By understanding the steel manufacturing process, we can understand better the importance of this vital material and its role in shaping the world around us.