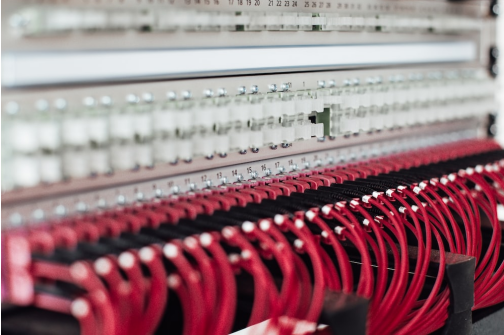
EVERYTHING YOU NEED TO KNOW ABOUT IIOT
Introduction
As digital transformation has emerged as a top priority for many companies operations, the phrase “the Industrial Internet of Things” has become increasingly commonplace in the context of the business world. So, what exactly is the IIoT?
The Industrial Internet of Things (IIoT), more commonly referred to as the Industrial Internet, is a network that connects vital resources, highly developed predictive and prescriptive analytics, and contemporary personnel in industrial settings. Systems that are able to monitor, collect, exchange, evaluate, and give valuable new insights in a way that has never been possible before can be attributed to the network of a multiplicity of industrial devices that are connected by communications technologies. These insights can then assist industrial organizations in making decisions that are more intelligent and more expedient for their businesses.
Revolutionary Impact
The IIoT has had a revolutionary impact on the manufacturing sector, altering the day-to-day operations of industrial corporations. The Industrial Internet of Things (IIoT) and the software solutions that are powered by it are driving powerful business outcomes. These outcomes include enabling Industrial AI to detect corrosion inside of a refinery pipe, providing real-time production data to uncover additional capacity in a plant, and accelerating the development of new products by feeding operations and service data back into the product design cycle. These are just a few examples.
The Industrial Internet of Things (IIoT) is enabling levels of productivity, efficiency, and performance that have never been seen before by merging machine-to-machine connectivity with industrial data analytics. And as a direct consequence of this, industrial enterprises operating in power generation, oil and gas, utilities, manufacturing, aviation, and a wide variety of other sectors are seeing revolutionary operational and financial gains.
Who was the first person to use the term “industrial internet”?
Late in 2012, GE was the company that first popularized the phrase “industrial internet.” GE is leading its own digital industrial transformation by capitalizing on the potential offered by the Industrial Internet of Things, also known as IIoT.
In addition, GE is assisting its customers in accelerating their digital transformation journeys by providing them with GE Digital’s portfolio of industrial software applications. These applications assist customers in resolving their most difficult problems by putting industrial data to use. This assistance is based on GE’s extensive experience as well as its deep expertise in both technology and the industry.
GE Digital is leveraging the power of the Industrial Internet of Things (IIoT) with software that transforms data into action by collaborating with customers, jumping into uncertainty, and applying rapid experimentation at speed and scale. This is being done at a time when the industrial world is getting ready for digitization.
As part of our mission to create a world that functions properly, we are putting focused artificial intelligence (AI) technologies to use to transform industrial assets and systems. As a result, these assets and systems are becoming more predictive, prescriptive, intelligent, and profitable. This includes the utilization of digital twins, which are learning and living models that integrate domain knowledge and physics with industrial artificial intelligence in order to detect, avoid, and predict crucial issues in order to reveal insights that produce commercial value. In addition, the remote capabilities made possible by the Industrial Internet assist crucial industries in the management of assets, the creation of operational systems, and the collection of data from any location on the planet.
What Are the Differences Between IoT and IIoT?
Both the Internet of Things (IoT) and the Industrial Internet of Things (IIoT) are fascinating technologies that hold the promise of bringing about significant change in a number of different aspects of industrial automation.
The following are some of the primary distinctions between IoT and IIoT:
The Internet of Things (IoT) is an ecosystem that connects various machines and devices through the use of a network. It could be a network of consumer wearables that are connected to one another and are used to monitor a limited number of electronic gadgets. In contrast, the Industrial Internet of Things (IIoT) refers to the process of improving an industrial company’s productivity, quality, and cost by utilizing data collected from connected equipment. As a consequence of this, it is typically intended to manage a significant volume of information.
Both the IoT and the IIoT are focused on improving business operations, while the IoT is more concerned with developing new applications and services that enhance the lives of consumers. While many of the Internet of Things devices are intended for use by people in their regular lives, the vast majority of the IIoT devices are created to assist businesses in operating more effectively.
Systems: The Internet of Things is dependent on cloud computing, whereas the Industrial Internet of Things (IIoT) does not require cloud computing because it makes use of local servers rather than remote servers. In addition, the IIoT platform is more secure than the IoT platform because it makes use of more well-established hardware and software platforms. These platforms have been put through extensive testing to ensure that they are resistant to being broken into by hackers. Click here to check out industrial IOT solutions examples.
Advantages of the Industrial Internet of Things
The most significant benefit of IIoT is that it enables manufacturers to automate their processes, which in turn allows them to improve the effectiveness of their working procedures. Robotics and other forms of automated technology can perform their tasks in a manner that is both more efficient and accurate, so contributing to an increase in overall manufacturing efficiency.
In addition, the software can be connected to physical machinery through the use of sensors, which can continuously check the performance of the gear. Because of this, manufacturers are able to gain deeper insights into the performance of individual pieces of equipment as well as the performance of entire fleets.