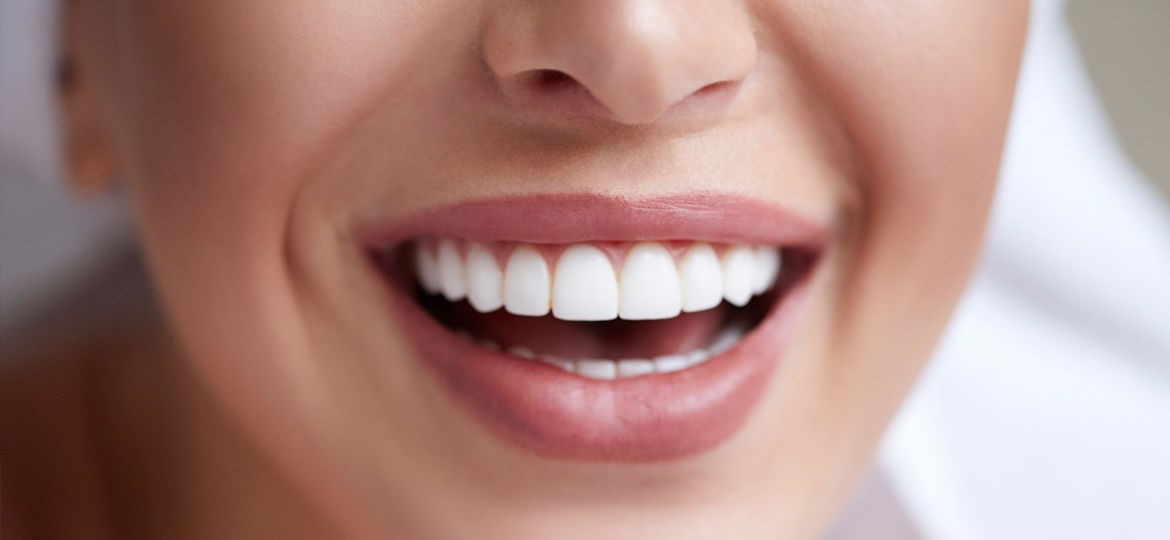
How do you make an Toothbrush from Design into Manufacturing
Introduction
A toothbrush is a vital instrument for maintaining good dental hygiene and overall health. The design and production process are constantly evolving with the incorporation of the latest materials and technology In this piece, we’ll explore the complex process that produces a toothbrush starting from the design stage through the manufacturing phase.
Design and Development
The manufacturing process of brush starts with careful design and creation. Designers take into consideration factors like the ergonomics of the toothbrush, bristle styles hand materials, as well as general aesthetics. The aim is to design an instrument that can be effective at cleansing teeth, but is also pleasant to use and visually attractive.
1. Selecting Bristles:
The bristles of a toothbrush come in different kinds of materials as well as firmness levels. They are soft, medium and hard bristles are suited to various oral hygiene needs and sensibilities. Also, Nylon bristles are widely used due to their toughness and pliability.
2. Handle The design:
Designers typically make use of computers-aided design (CAD) software to develop ergonomic brushes that sit comfortably within the palm and offer the precise control needed for the brushing process.
3. Material Selection:
The handles can be constructed from different materials like rubber, plastic, or bamboo to provide eco-friendly choices. Every material has its own unique characteristics to the toothbrush. These properties affect aspects like texture, weight and the impact on the environment.
4. Integrating Technology
A few toothbrushes have technological features such as vibrating bristles and timers to help ensure that the proper amount of time is spent on brushing. These functions are incorporated during the development phase in order to provide the smooth operation.
Materials and Manufacturing
After the design for the toothbrush is approved, the process of manufacturing commences. It involves identifying the right materials, creating production lines as well as adhering to the quality requirements.
1. Material Procurement
The chosen materials, such as bristles and handles can be purchased from vendors. Controlling quality is essential for ensuring that the components conform to the requirements in terms of safety and efficiency.
2. Injection Molding:
Injection molding is the most popular production process used for the manufacture of toothbrush handles. It is the very first step to make brush handles. Once the pellets of plastic are heated, they melt, they’re then placed into the mold cavity. When they have cooled, and solidified the mold slid open to let out the handle of the toothbrush.
3. Bristle Planting:
The bristles are secured to the hole using a variety of techniques, such as staple technology, and anchorless tufting. These techniques secure the bristles to guarantee that they stay in place when used.
4. Assembling Components
If the toothbrush has extra components such as grips with rubber or technology components they are attached to the handle at this point of manufacture.
5. Quality Control
Controls of quality are carried out throughout the production process. Included are an injection mold that is certified for the handle of the brush, inspection of the cleanness of bristles and an examination for the firmness of bristles. The tests ensure that every brush meets the requirements for safety and quality prior to it being packaged.
packaging and distribution
Packaging is a crucial element in maintaining the integrity of the toothbrush as well as providing pertinent information to the customer. The distribution network also ensures that the toothbrush is delivered to its market.
1. Packaging Design:
The packaging is designed not just protect the toothbrush, but also draw attention to consumers. The brush’s benefits, features and instructions for use are available on the box.
2. Environment-related Considerations
With increasing awareness of the environment companies are making green packaging methods, cutting down on usage of plastic and encouraging recycle.
3. Marketing and Distribution
The toothbrush is sold through a variety of ways, such as the retail store, on-line platforms and even dental clinics. The marketing efforts are designed to educate the consumer on the distinct features and benefits, which helps them make an informed choice.
New Trends in the Future as well as Innovations
The market for toothbrushes is constantly evolving, taking into account advances in technology and environmentally eco-friendly methods.
1. Smart Toothbrushes:
Through the use of sensors and communication smart toothbrushes will give real-time feedback about how well you brush and the duration of your session and can help improve the routine of oral hygiene.
2. Biodegradable Materials:
Innovative biodegradable products provide a green alternative to plastic toothbrushes. They address the increasing issue of the waste of plastic.
3. 3D Printing:
3-D printing lets the creation of customized toothbrush designs as well as rapid prototyping. This allows for greater customization and creativity in manufacture.
Oralgos OEM production
A reputable producer of dental irrigators and toothbrushes and water flosser Oralgos offers a variety of manual brushes, Extra soft toothbrush electric toothbrush gum toothbrush wholesale as well as customized OEM products at factory-priced. We can provide very affordable rates and will be happy to cooperate together with our customers.
Final
The process of making a toothbrush requires an intricate process from concept as well as development through production and distribution. A combination of modern technology and conventional practices makes sure that toothbrushes will continue to develop in response to the constantly changing demands of customers. While sustainability and the advancement of technology take place in the forefront, the sector is set to see new and exciting innovations that are set to redefine dental hygiene for the generations to come.