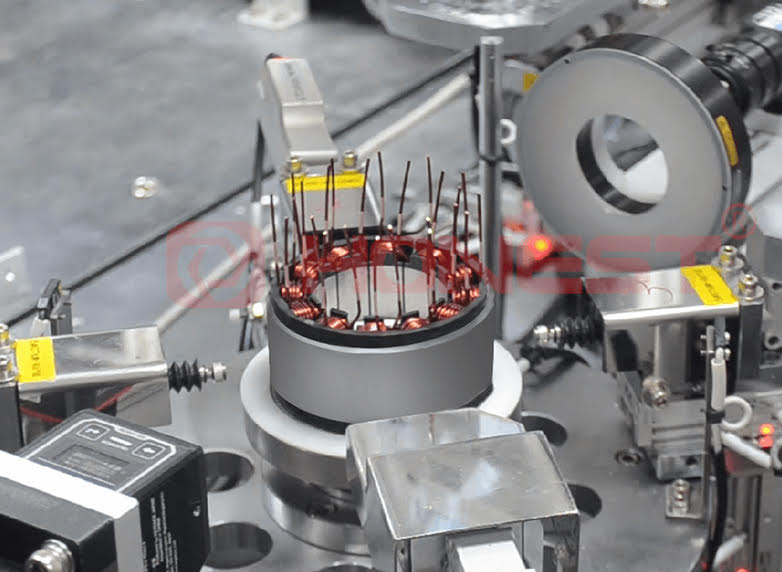
A Comprehensive Guide to Electric Motor Winding Machines
Introduction:
Electric motor winding machines play a crucial role in the manufacturing process of electric motors. These machines ensure the precise winding of wires around the motor’s core, enabling the motor to generate rotational power. In this article, we will delve into electric motor winding machines, exploring their various aspects, benefits, and functionality. Whether you are a professional in the industry or simply curious about electric motor winding machines, this guide aims to provide you with comprehensive insights and answers to your burning questions.
Understanding Electric Motor Winding Machines.
Electric motor winding machine is a specialized equipment designed to automate the winding process of electric motor coils. These machines enable efficient and precise winding of wires onto the motor’s core, ensuring optimal performance and longevity. By automating the winding process, manufacturers can significantly increase productivity while maintaining consistent quality standards.
Types of Electric Motor Winding Machines.
There are various types of electric motor winding machines available in the market. These include:
Automatic Coil Winding Machines:
These machines automate the winding process, from wire tensioning to coil formation. They offer high efficiency and precision, making them suitable for large-scale production.
Manual Coil Winding Machines:
These machines require manual intervention for wire tensioning and coil formation. While they offer more control, they are typically used for small-scale production or specialized winding requirements.
Semi-Automatic Coil Winding Machines:
These machines combine the advantages of automatic and manual winding machines. They automate certain aspects of the winding process while allowing for manual adjustments and customization.
Key Components of Electric Motor Winding Machines.
Electric motor winding machines consist of several key components:
Winding Head: The winding head holds the wire spool and guides it during the winding process.
Tensioning System: This system maintains the appropriate tension in the wire, ensuring uniform winding.
Traverse Mechanism: The traverse mechanism moves the winding head back and forth, ensuring even wire distribution across the motor’s core.
Wire Cutter: The wire cutter trims the wire once the desired number of turns is achieved.
Control Panel: The control panel allows operators to set parameters, adjust settings, and monitor the winding process.
Factors to Consider When Choosing a Winding Machine.
When selecting an electric motor winding machine, several factors should be taken into account:
Motor Size: Consider the size and specifications of the motors you will be winding to ensure compatibility with the machine.
Winding Complexity: Different motors may require specific winding techniques. Choose a machine that can accommodate the required winding complexity.
Production Volume: Determine the expected production volume to select a machine that can meet your output requirements.
Automation Level: Evaluate the level of automation needed based on your production goals, labor costs, and quality standards.
How Electric Motor Winding Machines Work.
Electric motor winding machines operate by following a set of programmed instructions. Here’s a simplified overview of the typical winding process:
Wire Setup: The operator sets up the wire spool, aligning it with the winding head.
Parameter Configuration: The operator configures the machine settings, including the number of turns and winding speed.
Wire Insertion: The machine starts the winding process, guiding the wire from the spool onto the motor’s core.
Traverse Motion: The traverse mechanism moves the winding head back and forth, evenly distributing the wire across the core.
Wire Cutting: Once the desired number of turns is achieved, the machine cuts the wire using a wire cutter.
Coil Formation: The machine secures the wound coil, ensuring it stays in place during further assembly or testing.
Benefits of Using Electric Motor Winding Machines.
Using electric motor winding machines offers several advantages:
Increased Efficiency: Winding machines automate the process, reducing production time and increasing overall efficiency.
Improved Precision: The automated nature of these machines ensures consistent and precise winding, resulting in high-quality motor coils.
Labor Cost Reduction: By minimizing manual labor requirements, manufacturers can lower production costs and allocate resources more efficiently.
Enhanced Productivity: Winding machines enable higher production volumes, allowing manufacturers to meet market demands more effectively.
Troubleshooting Common Issues with Winding Machines.
Despite their efficiency, electric motor winding machines may encounter occasional issues. Here are some common problems and their possible solutions:
Wire Tension Problems: Ensure the tensioning system is properly adjusted and the wire spool is correctly aligned.
Traverse Irregularities: Check the traverse mechanism for any obstructions or misalignments affecting its smooth operation.
Wire Breakage: Examine the wire path for sharp edges or other factors that may cause wire breakage. Adjust the wire tension if necessary.
Coil Misalignment: Verify that the traverse motion is properly calibrated to achieve an even wire distribution across the motor’s core.
Maintaining and Servicing Electric Motor Winding Machines.
To ensure optimal performance and longevity of electric motor winding machines, regular maintenance and servicing are essential. Follow these guidelines:
Lubrication: Keep the moving parts properly lubricated to minimize friction and ensure smooth operation.
Cleaning: Regularly clean the machine, removing dust and debris that may affect its performance.
Calibration: Periodically calibrate the machine to maintain accurate winding parameters.
Component Inspection: Check key components for wear and tear and replace them as needed to prevent unexpected breakdowns.
FAQs.
Q: How do electric motor winding machines improve productivity?
Electric motor winding machines automate the winding process, reducing the time required for each coil and allowing for higher production volumes. By minimizing manual labor, these machines significantly increase productivity.
Q: Can electric motor winding machines accommodate different wire sizes?
Yes, electric motor winding machines are designed to handle various wire sizes. Manufacturers provide different wire guides and tensioning systems to accommodate the desired wire diameter.
Q: Are electric motor winding machines suitable for small-scale production?
Yes, there are winding machines available for small-scale production. Manual and semi-automatic winding machines can be a cost-effective solution for smaller volumes.
Q: How long does it take to set up and calibrate an electric motor winding machine?
The setup and calibration time depend on the complexity of the winding machine and the operator’s familiarity with the process. On average, it may take a few hours to set up and calibrate a new machine.
Q: Can winding machines handle complex winding patterns?
Yes, modern winding machines, especially those equipped with CNC technology, can handle complex winding patterns. These machines allow for precise control of winding parameters, enabling customization.
Q: How often should an electric motor winding machine undergo maintenance?
Regular maintenance should be conducted based on the manufacturer’s recommendations and the machine’s usage. It is advisable to schedule maintenance every 6 to 12 months.
Conclusion.
Electric motors and needle winding machines are indispensable tools in the manufacturing industry. These machines automate the winding process, ensuring efficient production, consistent quality, and enhanced precision in electric motor coils. In this comprehensive guide, we have explored various aspects of electric motor winding machines, including their types, benefits, operation, and future developments.
We have also discussed the significance of precision in winding and the advancements in needle winding technology. With the knowledge gained from this article, you are now equipped to make informed decisions when it comes to selecting, using, and optimizing electric motor winding machines and needle winding machine. Incorporating these advanced machines into your production process can greatly enhance productivity, improve quality, and contribute to the overall success of your operations. So, embrace the power of electric motor winding machines and needle winding machines to elevate your manufacturing capabilities and stay ahead in the competitive market.