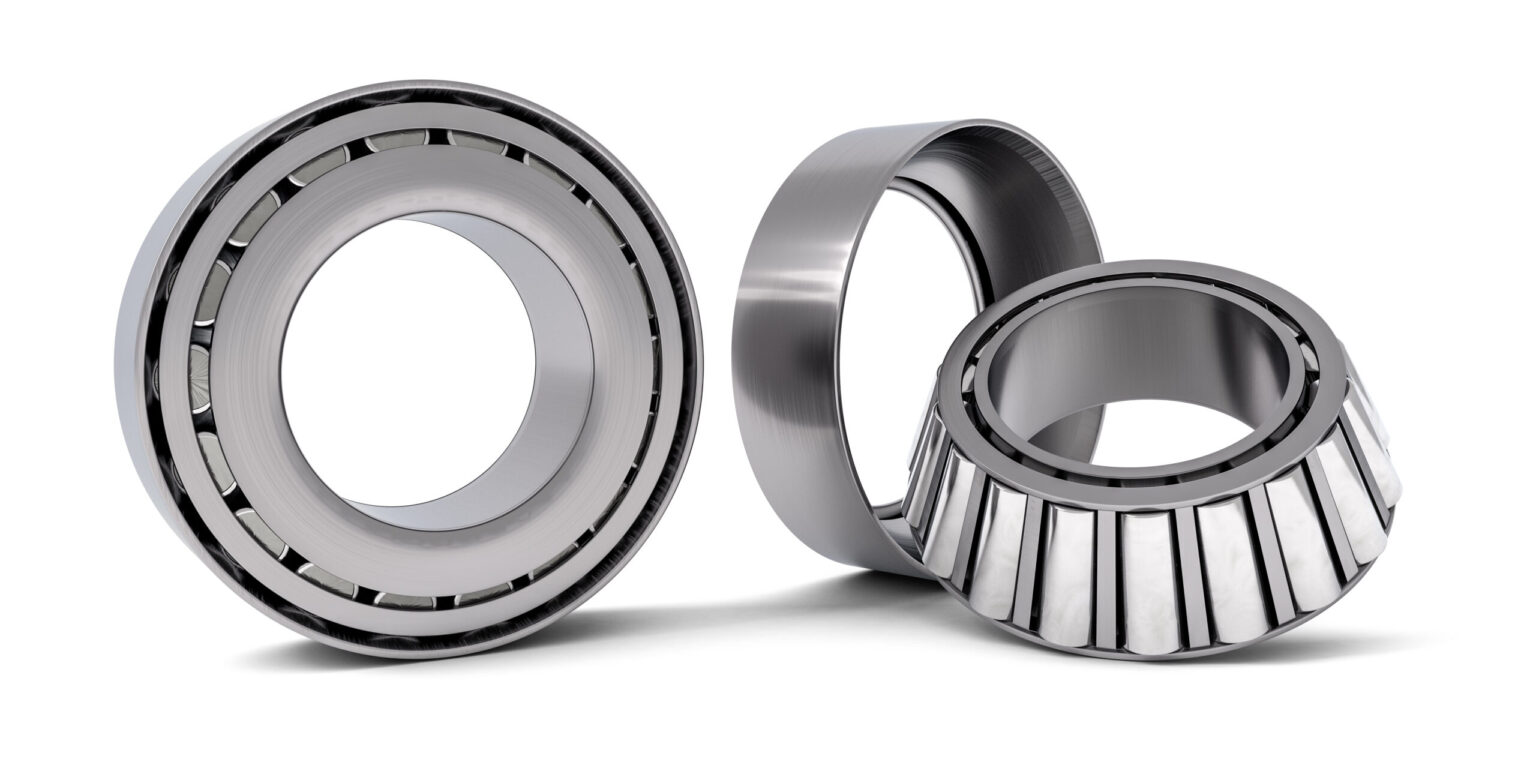
Applications of Roller Bearings in Various Industries
Roller bearings play a crucial role in numerous industries where rotational motion and load support are essential. Their ability to handle heavy loads, operate at high speeds, and provide smooth motion makes them indispensable in various applications. Here are some common industries where roller bearings find extensive use:
- Construction and Mining: Roller bearings are vital in construction and mining equipment, such as excavators, bulldozers, cranes, and crushers. They provide robust support for rotating components, allowing heavy machinery to handle extreme loads and operate in demanding environments while ensuring reliability and durability.
- Medical Equipment: Roller bearings are used in medical equipment, including imaging machines, surgical tools, and diagnostic devices. They facilitate precise and smooth movement in medical instruments, contributing to accurate diagnoses, minimally invasive procedures, and patient comfort.
- Renewable Energy: Roller bearings play a crucial role in renewable energy systems, such as wind turbines and solar tracking systems. They enable efficient rotation, support heavy turbine blades, and withstand challenging weather conditions, ensuring reliable and sustainable power generation.
- Robotics and Automation: Roller bearings are essential components in robotics and automation systems, enabling precise and smooth motion in robotic arms, linear actuators, and automated machinery. They provide the necessary support for accurate positioning and reliable operation of robotic systems.
MBY Bearing is a renowned manufacturer committed to delivering high-quality roller bearings and providing innovative solutions to meet the diverse needs of industries worldwide. The company’s unwavering dedication to quality, reliability, and continuous improvement sets it apart in the competitive bearing industry. These are just a few examples of the wide-ranging applications of roller bearings across various industries. Their versatility, durability, and ability to handle heavy loads and high speeds make them indispensable for achieving efficient and reliable mechanical motion in numerous industrial sectors.
Manufacturing Processes for Roller Bearings:
Roller bearings are manufactured using specific materials and manufacturing processes to ensure their durability, reliability, and performance. The selection of materials and manufacturing techniques depends on factors such as load capacity, speed requirements, operating conditions, and cost considerations. Here are some common materials and manufacturing processes used in the production of roller bearings:
The manufacturing process for roller bearings typically involves precision machining. Machining processes, such as turning, milling, and grinding, are used to shape the bearing components, including the inner and outer rings, rollers, and cages. Precision machining ensures the dimensional accuracy and surface finish required for proper bearing operation.
Heat treatment helps optimize the bearing’s ability to withstand heavy loads and resist fatigue failure.
Roller bearings are assembled by fitting the components together with precision. This includes assembling the inner and outer rings, installing the rollers, and positioning the cage. Lubrication methods can vary, including oil bath lubrication, grease packing, or applying lubricant during assembly.
Stringent quality control measures are implemented throughout the manufacturing process to ensure the reliability and performance of roller bearings. This includes dimensional inspections, hardness testing, surface finish evaluations, and functional testing of the assembled bearings. Quality control processes help identify and rectify any manufacturing defects or deviations.
It’s important to note that advancements in material science and manufacturing technologies continue to drive innovation in roller bearing production. New materials, such as advanced composites or hybrid designs combining different materials, are being explored to further enhance bearing performance in specific applications.
Maintenance of Roller Bearings:
Proper maintenance is essential to ensure the optimal performance and longevity of roller bearings. Regular maintenance practices help prevent premature wear, reduce downtime, and maximize the reliability of machinery and equipment. Here are some key maintenance steps for roller bearings:
1. Lubrication:
Adequate lubrication is crucial for the smooth operation of roller bearings. Follow the manufacturer’s recommendations for the correct lubricant type, viscosity, and replenishment interval. Regularly monitor the lubricant level and condition, and replenish or replace it as needed. Proper lubrication helps reduce friction, dissipate heat, and prevent premature wear.
2. Contamination Control:
Protecting roller bearings from contamination is vital. Implement effective sealing mechanisms, such as shields or seals, to prevent the ingress of dust, dirt, moisture, and other contaminants. Regularly inspect and clean the surrounding area to minimize the risk of contamination. If contamination occurs, clean the bearing carefully following appropriate procedures, and replace the lubricant.
3. Temperature Monitoring:
Monitoring the operating temperature of roller bearings is essential to detect potential issues. Excessive heat can indicate problems such as inadequate lubrication, overloading, or misalignment. Use temperature monitoring devices to regularly check the bearing temperature and compare it to recommended limits. Investigate and address any abnormal temperature rise promptly.
4. Vibration Analysis:
Regular vibration analysis helps identify potential bearing problems early. Use vibration monitoring equipment to measure and analyze vibration levels. Unusual vibration patterns or increases in vibration intensity may indicate issues such as misalignment, bearing wear, or insufficient lubrication. Take appropriate action based on the vibration analysis results.
5. Inspection and Replacement:
Conduct routine inspections of roller bearings to check for signs of wear, damage, or abnormal conditions. Inspect the bearing’s outer and inner surfaces, raceways, cages, and rolling elements. Look for indications of pitting, scoring, rust, or excessive play. If any abnormalities are detected, consider replacing the bearing promptly to prevent further damage or failure.
6. Proper Handling and Storage:
Handle and store roller bearings with care to avoid damage. Follow proper procedures for lifting, transporting, and installing bearings. Protect them from impacts, shocks, and exposure to moisture or corrosive substances. Store bearings in a clean and dry environment, away from direct sunlight, extreme temperatures, and vibrations.
7. Training and Documentation:
Ensure that maintenance personnel receives proper training on roller bearing maintenance procedures and best practices. Maintain comprehensive documentation of maintenance activities, including lubrication schedules, inspection records, and replacement history. This documentation aids in tracking maintenance activities and identifying trends or recurring issues.
8. Collaborate with Suppliers:
Establish a collaborative relationship with bearing suppliers or manufacturers. Seek their expertise and guidance in selecting the right bearing types, lubricants, and maintenance practices for specific applications. Stay updated with the latest advancements in bearing technology and follow recommended maintenance guidelines provided by the suppliers.
By following these maintenance practices, engineers and maintenance personnel can effectively care for roller bearings, prolong their service life, and ensure their reliable performance in various industrial applications. Regular monitoring, lubrication, contamination control, inspections, and proper handling contribute to the overall efficiency and productivity of machinery and equipment.
Innovations and Advancements in Roller Bearing Technology:
Roller-bearing technology has seen significant advancements in recent years, driven by the need for improved performance, efficiency, and reliability in various industries. These innovations aim to address challenges such as high loads, high speeds, harsh operating conditions, and extended service life. Here are some notable advancements in roller-bearing technology:
- Ceramic Roller Bearings: Ceramic roller bearings, made from materials like silicon nitride (Si3N4) or zirconia (ZrO2), have gained popularity in applications requiring high-speed operation, electrical insulation, and resistance to corrosion. Ceramic rollers offer lower friction, reduced heat generation, and improved wear resistance compared to traditional steel rollers, resulting in enhanced performance and longer bearing life.
- Sealing and Lubrication Innovations: Advancements in sealing technologies have led to improved protection against contamination and extended bearing life.
- Sensor Integration: Sensor-equipped bearings provide valuable data on bearing condition and performance, enabling predictive maintenance strategies and reducing the risk of unexpected failures.
- Computational Modeling and Simulation: Advanced software tools allow engineers to analyze and optimize bearing geometry, material selection, and lubrication parameters virtually. This helps to shorten development cycles, improve performance predictions, and reduce costs associated with physical prototypes and testing.
These innovations and advancements in roller-bearing technology continue to push the boundaries of performance and reliability. By incorporating these advancements into their designs, engineers and manufacturers can develop roller bearings that meet the evolving demands of various industries, providing improved efficiency, reduced downtime, and extended service life.
Conclusion: The Significance of Roller Bearings in Modern Machinery and Engineering
In conclusion, MBY Bearing stands out for its unwavering commitment to quality, innovation, customer satisfaction, and environmental responsibility. With a focus on delivering high-performance roller bearings and innovative solutions, MBY Bearing continues to be a trusted partner for industries across the globe. Innovations such as ceramic and hybrid roller bearings offer enhanced speed capabilities, reduced friction, and extended service life, contributing to improved machinery performance and productivity. Sealing and lubrication advancements ensure better protection against contaminants, minimizing the risk of premature wear and failure. Sensor integration enables real-time monitoring, allowing for predictive maintenance strategies and increased equipment uptime.
In modern engineering, roller bearings are crucial for achieving precise and smooth motion, reducing friction and heat generation, and minimizing wear and tear. They provide stability, load distribution, and rotational accuracy, allowing machines to operate efficiently and reliably.